Vorschriften und Arbeitsschutz-Maßnahmen im Überblick
Lager sind komplexe Arbeitsumgebungen mit vielfältigen Gefahren – von umkippenden Regalen und Kollisionen mit Flurförderzeugen bis hin zu Brand- und Explosionsrisiken. Zudem können physische und psychische Belastungen die Gesundheit der Mitarbeitenden beeinträchtigen. Ein wirksamer Arbeitsschutz ist daher essenziell, um Unfälle zu vermeiden, sichere Arbeitsbedingungen zu schaffen und die Sicherheit zu gewährleisten. Die Einhaltung gesetzlicher Vorschriften sowie gezielte Schutzmaßnahmen tragen nicht nur zur Sicherheit bei, sondern optimieren auch betriebliche Abläufe. Welche Regelungen gelten für den Lagerbetrieb, und welche Maßnahmen helfen, Risiken zu minimieren? In unserem Beitrag geben wir Ihnen einen kompakten Überblick über die wichtigsten Vorschriften und bewährte Sicherheitsstrategien.
Gefahr erkannt, Gefahr gebannt: die typischen Gefahrenquellen im Lagerbereich
Ein unachtsamer Moment, ein kleiner Defekt oder eine falsche Bewegung – und schon kann es im Lager gefährlich werden. Gabelstapler und Scherenhubwagen fahren zwischen den Regalen hindurch, schwere Lasten werden gehoben und gelagert, elektrische Geräte sind im Dauereinsatz. Überall gibt es potenzielle Unfallquellen und Gefahrensituationen. Wer diese Risiken frühzeitig erkennt und beseitigt, schafft nicht nur eine sichere Arbeitsumgebung, sondern trägt auch zur Effizienz und Produktivität im Betrieb bei. Um die Gefahren zu minimieren, ist es also zunächst wichtig, die verschiedenen Risikofaktoren zu verstehen. Man kann in elektrische, chemische und strukturelle Risikoquellen unterteilen.
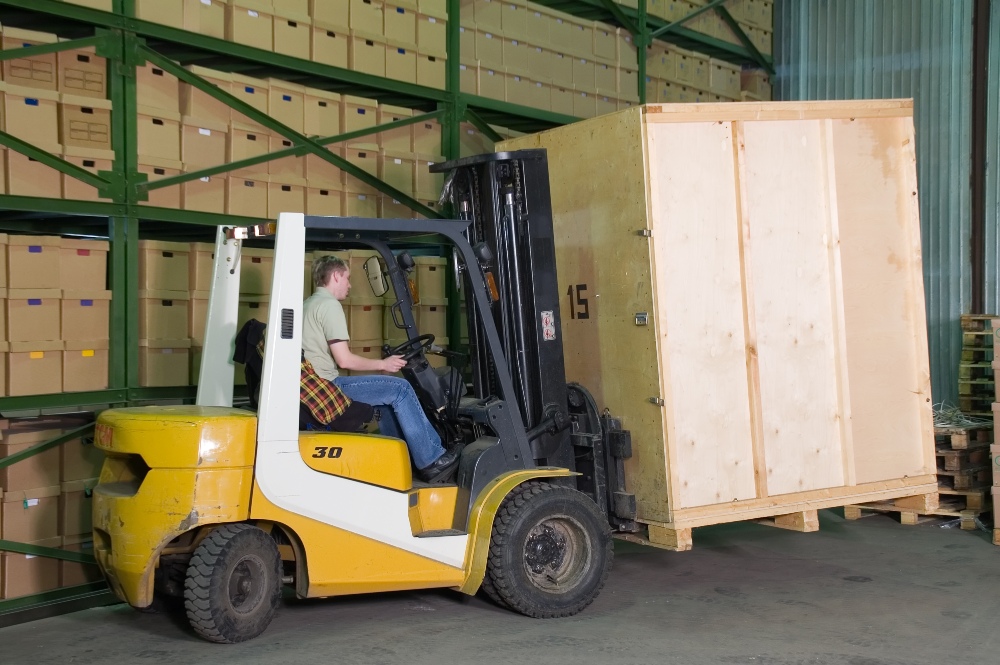
Mechanische Gefahrenquellen
Mechanische Risiken entstehen vor allem durch Transportgeräte und Arbeitsmittel. Unsachgemäß gesicherte oder defekte Gabelhubwagen, Stapler oder Lagermaterialwagen können schwere Unfälle verursachen. Auch scharfkantige Regale und rutschige Böden erhöhen das Verletzungsrisiko erheblich.
Gefahren durch elektrische Spannung
Elektrische Gefahren sind oft weniger sichtbar, aber nicht minder gefährlich. Defekte Kabel, überlastete Steckdosen oder fehlerhafte Ladestationen können Kurzschlüsse und Brände auslösen. Ein einziger Funke reicht aus, um große Schäden zu verursachen.
Chemische Risiken: Gefahrstoffe richtig handhaben
Die chemische Gefährdung entsteht, wenn Gefahrstoffe falsch gelagert oder unsachgemäß gehandhabt werden. Fehlen eindeutige Kennzeichnungen – etwa durch Sicht- und Kennzeichnungstaschen – oder Sicherheitsmaßnahmen, drohen Verätzungen, Vergiftungen oder Explosionen. In Lagerbetrieben, die mit brennbaren oder toxischen Substanzen arbeiten, sind natürlich auch besondere Vorsichtsmaßnahmen erforderlich.
Strukturelle Risikoquellen
Auch bauliche Mängel und Lagerstrukturen stellen eine erhebliche Gefahr dar. Überladene oder instabile Regalsysteme können kippen oder einstürzen, herabfallende Waren gefährden Mitarbeitende und verursachen Sachschäden. Hinzu kommen Stolperfallen, fehlende Lagerregalbeschilderungen und unzureichende Beleuchtung, die das Unfallrisiko weiter erhöhen.
Welche Sicherheitsbestimmungen im Lager gibt es?
Die Vielzahl an Risiken im Lager macht deutlich, wie wichtig umfassende Sicherheitsmaßnahmen sind. Auch der Gesetzgeber und Berufsgenossenschaften tragen diesem hohen Gefahrenpotenzial Rechnung und haben besondere Vorgaben formuliert, um Unfälle zu verhindern und die Arbeitsbedingungen zu verbessern. Unternehmen sind daher verpflichtet, sich an spezifische Vorschriften zu halten, die sowohl den Umgang mit Arbeitsmitteln als auch die Gestaltung der Lagerumgebung regeln. Diese rechtlichen Grundlagen definieren nicht nur die Verantwortung von Arbeitgebern und Beschäftigten, sondern bieten auch konkrete Leitlinien für einen sicheren Betrieb. Zu den wichtigsten Vorschriften gehören:
- Arbeitsschutzgesetz (ArbSchG) – Definiert die grundlegenden Pflichten von Arbeitgebern und Arbeitnehmern im Arbeitsschutz.
- Betriebssicherheitsverordnung (BetrSichV) – Enthält Vorgaben zur sicheren Nutzung von Arbeitsmitteln und Maschinen.
- Arbeitsstättenverordnung (ArbStättV) – Legt fest, wie Arbeitsplätze und Lagerbereiche sicher und gesundheitsgerecht gestaltet werden müssen.
- Unfallverhütungsvorschriften (UVV) der Deutschen Gesetzlichen Unfallversicherung (DGUV) – Verbindliche Vorschriften zur Vermeidung von Unfällen und Gesundheitsschäden im Lager. Auf einzelne DGUV-Vorschriften, die für die Sicherheit im Lager besonders wichtig sind, wird später noch detailliert eingegangen.
- Technische Regeln für Betriebssicherheit (TRBS) – Beschreiben, wie die Anforderungen der Betriebssicherheitsverordnung in der Praxis umgesetzt werden können, insbesondere im Umgang mit Arbeitsmitteln und Anlagen.
- Technische Regeln für Arbeitsstätten (ASR) – Ergänzen die Arbeitsstättenverordnung und enthalten detaillierte Vorgaben zu Beleuchtung, Verkehrswegen, Flucht- und Rettungswegen sowie zur optimalen Nutzung von Lagerflächen.
- Berufsgenossenschaftliche Regeln (BGR) und Informationen (BGI) – Bieten branchenspezifische Sicherheitsanforderungen, beispielsweise für Lagerhaltung, Gefahrstofflagerung oder den sicheren Umgang mit Leitern und Tritten.
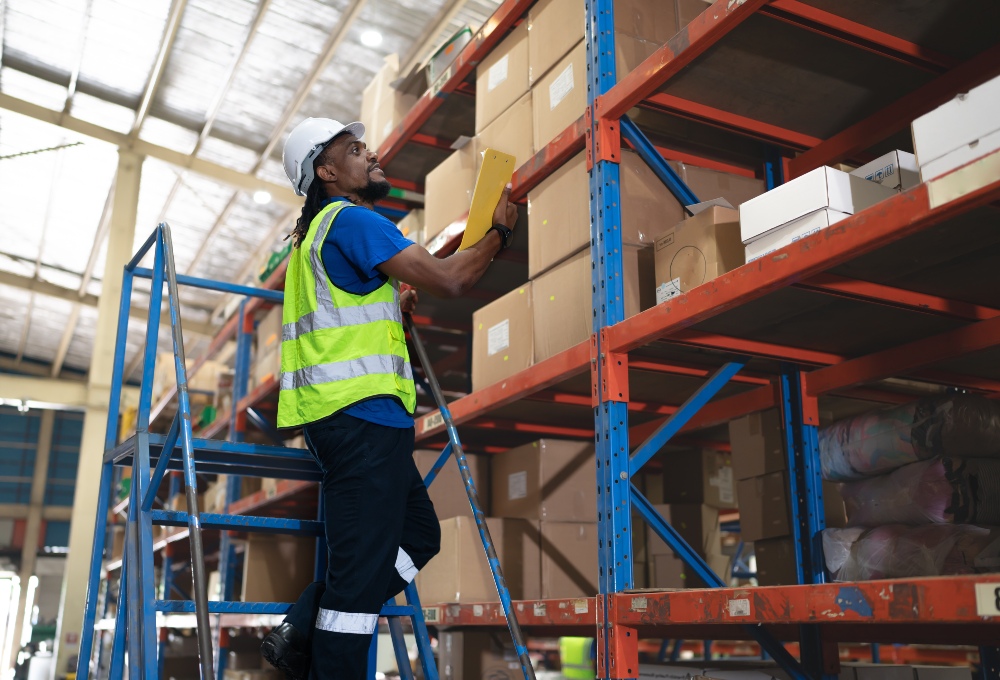
Ein wichtiger Bestandteil dieser Vorschriften ist die Arbeitsplatzkennzeichnung mit genormten Warnschildern und Gebotsaufklebern. Sie dient dazu, Gefahrenstellen eindeutig zu markieren, Verkehrswege zu regeln und Flucht- sowie Rettungswege klar auszuweisen. Die Vorgaben dazu sind insbesondere in der Arbeitsstättenverordnung (ArbStättV) und den Technischen Regeln für Arbeitsstätten (ASR) festgelegt. Eine gut sichtbare und normgerechte Beschilderung trägt erheblich zur Unfallvermeidung bei und erleichtert die Orientierung in komplexen Lagerstrukturen. Besonders in der Lagerlogistik spielen die Vorschriften der Deutschen Gesetzlichen Unfallversicherung eine entscheidende Rolle. Sie enthalten verbindliche Regelungen für den sicheren Umgang mit Lagereinrichtungen, Flurförderzeugen und anderen betrieblichen Risiken. Welche DGUV-Vorschriften speziell für die Lagerwirtschaft relevant sind und wie sie zur Unfallvermeidung beitragen, wird im folgenden Abschnitt genauer erläutert.
Vorschriften, Regeln und Grundsätze der Deutschen Gesetzlichen Unfallversicherung
Wie bereits erwähnt, spielt die Deutsche Gesetzliche Unfallversicherung eine entscheidende Rolle im Bereich der Lagerlogistik. Ihre Vorschriften, Regeln und Grundsätze gehen gezielt auf die besonderen Gefahren in Lagerbetrieben ein und bieten klare Vorgaben für einen sicheren Arbeitsalltag. Während die DGUV-Vorschriften rechtlich bindend sind, dienen die Regeln und Grundsätze als praxisnahe Leitlinien, um die gesetzlichen Bestimmungen bestmöglich umzusetzen.
Besonders relevant für die Sicherheit im Lager sind Regelungen zur Nutzung von Flurförderzeugen, zur Stabilität und Belastbarkeit von Lagereinrichtungen sowie zur Schulung von Staplerfahrern. Die DGUV Vorschrift 68 legt verbindliche Sicherheitsvorgaben für den Betrieb von Gabelstaplern und Hubwagen fest, während die DGUV Regel 108-007 detaillierte Anforderungen an die Stabilität und Belastbarkeit von Regalsystemen sowie die sichere Nutzung von Lagereinrichtungen enthält. Ergänzend dazu definiert der Grundsatz 308-001 der Deutschen Gesetzlichen Unfallversicherung, welche Schulungsanforderungen für Staplerfahrer gelten, um eine sichere Bedienung von Flurförderzeugen zu gewährleisten.
Neben diesen spezifischen Vorschriften deckt das DGUV-Regelwerk weitere essenzielle Aspekte des Arbeitsschutzes ab. Die DGUV Vorschrift 1 gibt allgemeine Grundsätze zur Prävention vor, während die Vorschrift 79 der Deutschen Gesetzlichen Unfallversicherung klare Regeln für die Nutzung persönlicher Schutzausrüstung (PSA) enthält. Die DGUV Regel 100-500 beschreibt die sichere Nutzung von Arbeitsmitteln, und die DGUV Regel 112-189 ergänzt dies durch spezifische Anforderungen an Schutzkleidung. Im Bereich Brandschutz und Explosionsprävention enthält die Regel 113-004 der Deutschen Gesetzlichen Unfallversicherung wichtige Maßnahmen zur Gefahrenvermeidung in Lagerbereichen, in denen entzündliche Stoffe vorhanden sind.
Gerade im Brandschutz sind präventive Maßnahmen unerlässlich, um im Ernstfall Schlimmeres zu verhindern. Ein wesentlicher Bestandteil ist dabei die Kennzeichnung von Rettungswegen mit Fluchtwegsaufklebern, die sowohl in der DGUV Information 211-041 als auch in den Technischen Regeln für Arbeitsstätten (ASR A1.3 – Sicherheits- und Gesundheitsschutzkennzeichnung) geregelt ist. Notausgänge, Fluchtwege und Sammelstellen müssen mit genormten Schildern und Aufklebern eindeutig markiert sein, um eine schnelle und geordnete Evakuierung zu gewährleisten. Ergänzend dazu schreibt der DGUV Grundsatz 309-003 vor, dass Regalsysteme regelmäßig sicherheitstechnisch geprüft werden müssen, um Stabilität und Tragfähigkeit zu gewährleisten.
Gefährdungsbeurteilung und Sicherheitskonzept nach dem STOP-Prinzip
Die Einhaltung der Vorschriften, Regeln und Grundsätze der Deutschen Gesetzlichen Unfallversicherung schafft eine solide Grundlage für mehr Sicherheit im Lager. Doch um Risiken nicht nur zu erkennen, sondern gezielt zu minimieren, sind weiterführende Maßnahmen erforderlich. Gesetzliche Vorgaben allein reichen nicht aus – sie müssen in der Praxis mit einem durchdachten Sicherheitskonzept umgesetzt werden.
Ein zentraler Baustein dabei ist die Gefährdungsbeurteilung, die Unternehmen hilft, potenzielle Risiken frühzeitig zu identifizieren und geeignete Schutzmaßnahmen abzuleiten. Gemäß §5 des Arbeitsschutzgesetzes (ArbSchG) sind Betriebe verpflichtet, regelmäßig eine systematische Analyse aller Arbeitsbereiche durchzuführen. Dabei gilt es nicht nur bestehende Gefahren zu bewerten, sondern auch betriebliche Veränderungen – sei es durch neue Maschinen, Umbauten oder Unfälle – in die Sicherheitsstrategie zu integrieren.
Bei einer Gefährdungsbeurteilung im Lager müssen alle sicherheitsrelevanten Bereiche berücksichtigt werden. Dazu gehören Regale und Paletten, Maschinen und Fahrzeuge, Arbeitsmaterialien, Verkehrswege sowie stationäre Arbeitsplätze. Ziel ist es, das Gefahrenpotenzial systematisch anhand definierter Kriterien einzuschätzen. Auf Basis dieser Erkenntnisse werden gezielt Schutzmaßnahmen entwickelt, um Risiken zu minimieren oder vollständig zu beseitigen und die Sicherheit zu erhöhen. Neben offensichtlichen physischen Gefahren spielen auch psychische Belastungen eine Rolle. Monotone Arbeitsabläufe, unzureichende Beleuchtung oder fehlende Pausenzeiten können langfristig die Gesundheit der Mitarbeitenden beeinträchtigen und sollten daher ebenfalls in die Beurteilung einfließen. Die Verantwortung für die Durchführung der Gefährdungsbeurteilung liegt bei der Betriebsleitung. Wer über die erforderlichen Fachkenntnisse verfügt, kann die Analyse intern durchführen. Alternativ empfiehlt es sich, eine interne oder externe Fachkraft für Arbeitssicherheit hinzuzuziehen, um eine fachgerechte Bewertung und Umsetzung sicherzustellen.
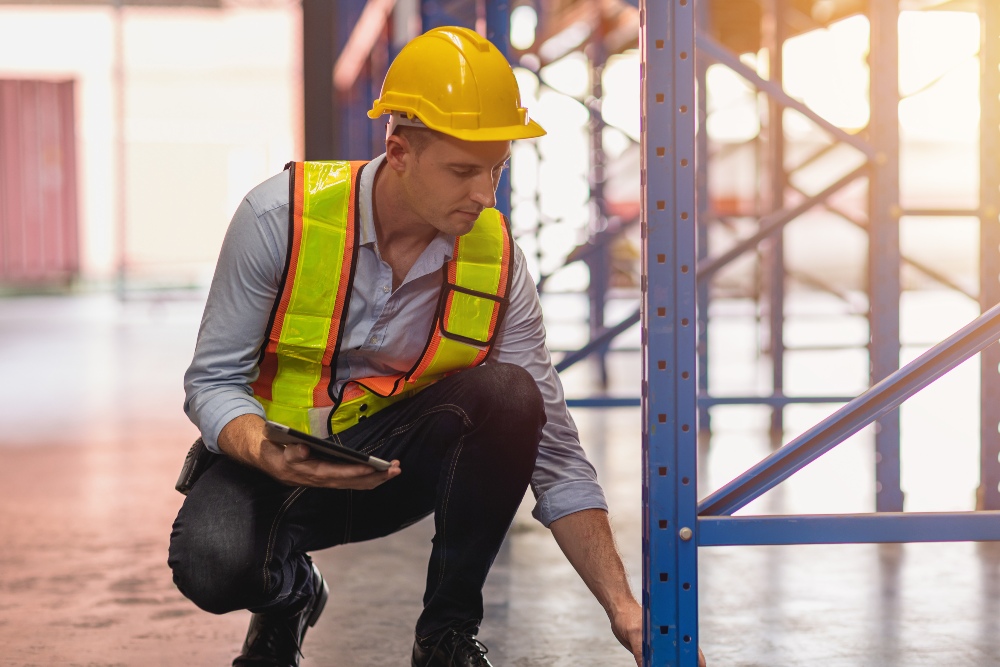
STOP-Prinzip als Grundlage für mehr Sicherheit im Lager
Die Gefährdungsbeurteilung liefert wertvolle Erkenntnisse über potenzielle Risiken im Lager. Doch um diese Gefahren gezielt zu minimieren und die Sicherheit zu maximieren, braucht es ein durchdachtes Sicherheitskonzept. Bereits bei der Lagerplanung sollten wesentliche Maßnahmen berücksichtigt werden, um Unfälle und gesundheitliche Beeinträchtigungen zu vermeiden. Dazu gehören:
- Eine sinnvolle Lagergestaltung, um Engstellen und Gefahrenquellen zu reduzieren.
- Die Auswahl geeigneter Maschinen und Arbeitsgeräte, die den Sicherheitsanforderungen entsprechen.
- Die Optimierung von Arbeitsabläufen, um Kollisionen und unnötige Risiken zu vermeiden.
- Die Schulung der Mitarbeitenden sowie die Bereitstellung von Schutzkleidung und Sicherheitsausrüstung.
Eine besonders wirksame Methode zur Verbesserung der Sicherheit ist das STOP-Prinzip. Dieses Modell hilft, Gefahren systematisch zu reduzieren und lässt sich in vier zentrale Maßnahmen unterteilen:
- Substitution: Gefährliche Stoffe, Maschinen, Transportgeräte oder Verfahren durch sicherere Alternativen ersetzen.
- Technik: Bauliche und technische Anpassungen vornehmen, um Risiken zu minimieren (z. B. rutschfeste Böden, Schutzeinrichtungen).
- Organisation: Arbeitsprozesse so strukturieren, dass Sicherheit und Effizienz gleichermaßen gewährleistet sind.
- Personal: Mitarbeitende befähigen, Gefahren frühzeitig zu erkennen und sicher zu handeln.
Beispiel: Ein Unternehmen, das alte, störanfällige Maschinen durch moderne, zertifizierte Anlagen ersetzt, rutschfeste Böden installiert, Verkehrswege mit Leitsystem-Klebern und Warnaufklebern klar kennzeichnet, die Arbeitsabläufe effizient strukturiert und seine Mitarbeitenden regelmäßig schult, verringert das Unfallrisiko erheblich. Dadurch erhöht das Unternehmen nicht nur die Sicherheit seiner Belegschaft, sondern minimiert auch Sachschäden und Produktionsausfälle.
3 praktische Tipps für mehr Sicherheit im Lager – von der Wartung bis zur Kennzeichnung
Welche Maßnahmen tragen konkret zur Sicherheit im Lager bei? Je nach Betrieb unterscheiden sich die Anforderungen, doch einige grundlegende Sicherheitsmaßnahmen sind in jeder Lagerumgebung unerlässlich. Dazu zählen die regelmäßige Wartung von Flurförderfahrzeugen, die Prüfung von Regalsystemen und die klare Kennzeichnung potenzieller Gefahrenbereiche.
Gabelstapler und andere Transportgeräte regelmäßig warten
Flurförderfahrzeuge wie Gabelstapler, Hubwagen, Schwerlast-Transportwagen und andere Transportgeräte müssen jederzeit betriebsbereit und sicher sein. Um dies zu gewährleisten, sollten diese täglich auf Beschädigungen, Funktionsstörungen und mögliche Sicherheitsmängel überprüft werden. Zusätzlich ist eine regelmäßige, professionelle Wartung nach Herstellerangaben erforderlich. Eine lückenlose Dokumentation der Prüfungen hilft, Probleme frühzeitig zu erkennen und ungeplante Ausfälle zu vermeiden.
Regalsysteme kontinuierlich prüfen und sicher nutzen
Lagerregale müssen tragfähig, stabil und sicher sein. Eine gleichmäßige Lastverteilung ist essenziell, um ein Umkippen oder Zusammenbrechen zu verhindern. Unternehmen sollten sicherstellen, dass die zulässigen Fach- und Feldlasten nicht überschritten werden. Insbesondere Schwerlastregale müssen regelmäßig auf mögliche Verformungen, lockere Verbindungen oder strukturelle Schwächen geprüft werden. Hier empfiehlt sich eine jährliche Regalinspektion durch eine Fachkraft, wie es auch in der DIN EN 15635 (Regalprüfung) empfohlen wird.
Eindeutige Sicherheitskennzeichnung einsetzen
Eine klare und normgerechte Kennzeichnung von Regalen, Verkehrswegen und Gefahrenbereichen ist ein wesentlicher Bestandteil der Unfallprävention. Sicherheitskennzeichen wie Schilder, Bodenmarkierungen und Aufkleber sorgen für eine bessere Orientierung, mehr Sicherheit und reduzieren das Risiko von Fehlverhalten oder Unfällen.
Mit gezielten Maßnahmen Arbeitsschutz und Sicherheit im Lager maximieren
Ein sicheres Lager erfordert mehr als nur gesetzliche Vorschriften – es braucht eine konsequente Umsetzung im Arbeitsalltag. Die regelmäßige Wartung von Transportgeräten, die Kontrolle von Regalsystemen und eine eindeutige Sicherheitskennzeichnung sind essenzielle Maßnahmen, um Unfälle zu vermeiden. Wer auf zuverlässige Technik, eine durchdachte Organisation und geschulte Mitarbeitende setzt, schafft eine sichere Arbeitsumgebung und erhöht zugleich Sicherheit sowie die betriebliche Effizienz.